Safety is at the central core of NWPX’s culture and is ingrained at every level of our organization. More than just policy and procedure, our safety programs give equal focus to the human side of safety, integrating coaching and mentoring efforts with compliance-driven approaches. By instilling a deep commitment to safety that extends from our CEO to general laborers on the floor, we have consistently achieved industry-leading safety performance, while improving productivity and lowering costs.
As a manufacturer, we work hard to eliminate hazards associated with high-risk work such as falls, heavy equipment operation, lockouts, and tagouts. We also focus on personal safety issues, such as complacency and fatigue.
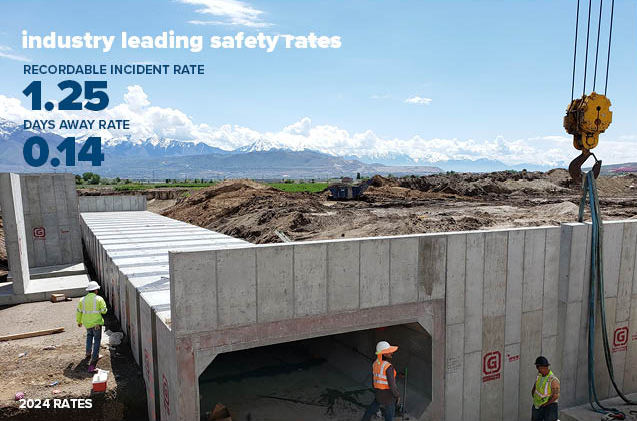
Setting a New Standard in Safety
Our unwavering commitment to the safety of our employees is reflected in our remarkable safety record. In 2024, all 13 of our plants had Recordable Incident and Days Away rates well below the national average, achieving some of the lowest rates ever seen at Northwest Pipe. We take pride in continuing this trend by providing ongoing training and fostering diligence on the part of every team member to guarantee a secure working environment for all.
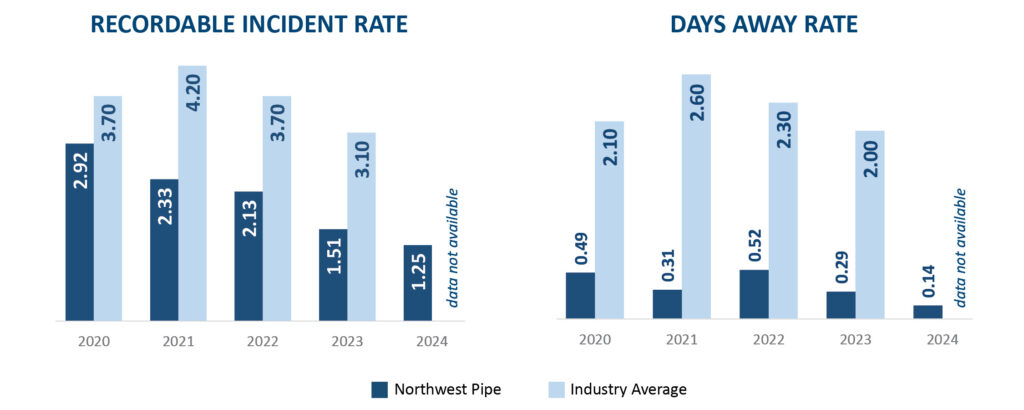
The Company’s Recordable Incident and Days Away rates are significantly lower than comparable industry averages. Industry average rates are recorded to OSHA per 100 full-time workers for SIC code 33121 (Iron and steel pipe and tube manufacturing from purchased steel).
Safety Programs
We are committed to moving and managing water in the most efficient and sustainable way, and that starts with protecting our people. We’re investing in cutting-edge training, modern equipment, and best-in-class protocols to create the safest workplaces in our industry.
Our operating standards empower every employee to speak up and take action when they spot a potential issue — because everyone has the right to a safe environment. We won’t stop until we achieve our ultimate goal: zero accidents.
Five to Stay Alive
The Five to Stay Alive Program is the latest innovation by our Director of Safety and Environmental Compliance. The program focuses on the top five most common safety hazards: forklifts and vehicles, ladders, fall protection, LOTO and machine guarding, and crane and rigging systems. Throughout the year, safety information is shared with our team via in-plant presentations, reminder hand-outs, our plant communications slide deck, and team one-on-ones. With additional awareness, we are working on mitigating the challenges of our working environment.
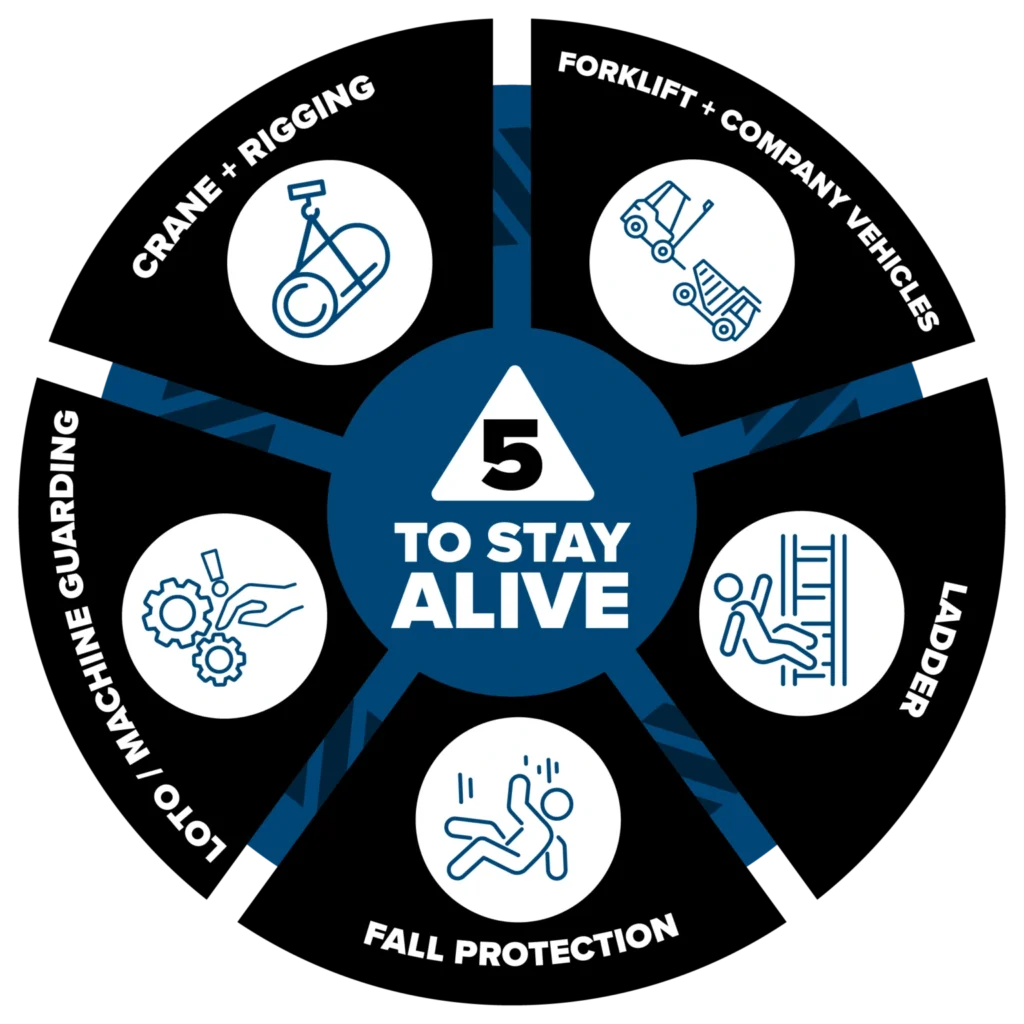
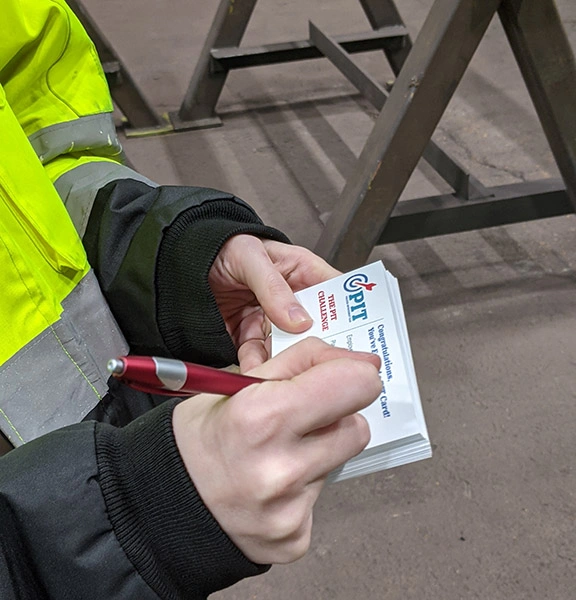
PIT Program
PIT has 100% employee participation at our legacy plants, meaning each employee has submitted at least one PIT card per quarter. The success of this program is credited to cash awards distributed to employees through a lottery-style system.
Lean in Action
To share our safety and process improvement successes between our plants, we established the Lean in Action Program. Each plant submits multiple Lean in Action improvements per year. Each report includes an assessment of the activity, photos, a before and after statement of how a process was improved, a summary of cost or labor hour savings associated with the action, and the overall benefits of the improved action.
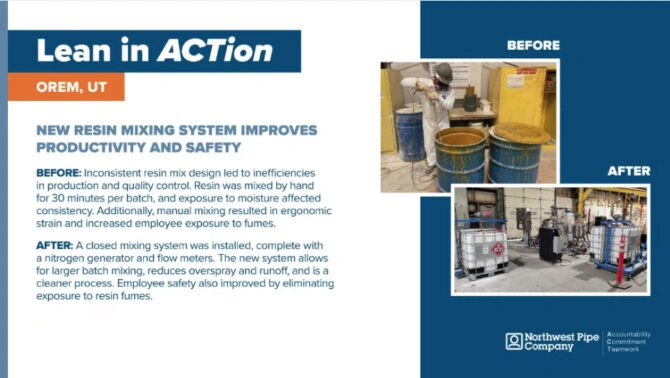